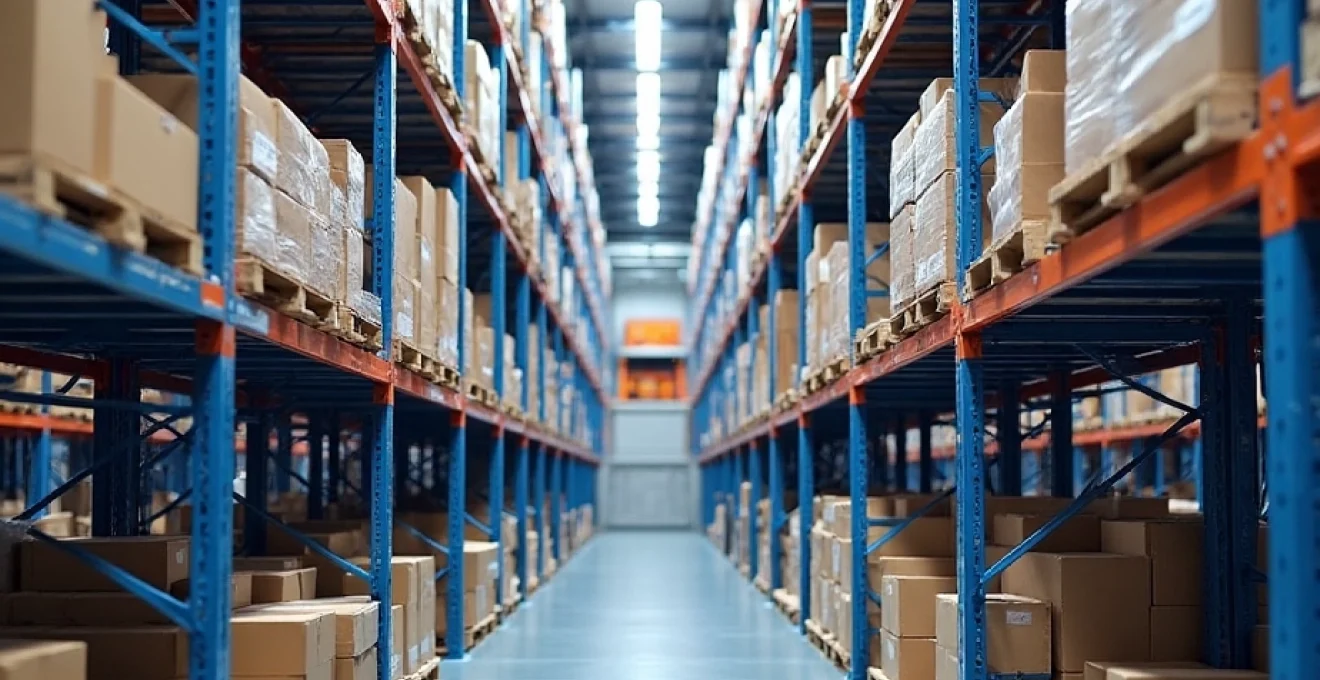
En el competitivo mundo de la logística y la gestión de almacenes, la eficiencia es clave para el éxito empresarial. Los sistemas de almacenamiento rotativo se han convertido en una solución innovadora para optimizar el espacio, reducir tiempos de picking y mejorar la productividad general. Estos sistemas aprovechan la altura y el movimiento circular para maximizar la capacidad de almacenamiento, ofreciendo una alternativa potente a los métodos tradicionales. Si busca revolucionar su logística y llevar la eficiencia de su almacén al siguiente nivel, es momento de considerar la implementación de un sistema de almacenamiento rotativo.
Fundamentos de los sistemas de almacenamiento rotativo vertical
Los sistemas de almacenamiento rotativo vertical son soluciones avanzadas que utilizan el principio de “producto al operario” para optimizar los procesos de picking y almacenamiento. Estos sistemas consisten en una serie de bandejas o estantes que rotan verticalmente, llevando los artículos directamente al punto de acceso del operario. Este enfoque elimina la necesidad de que los trabajadores se desplacen por el almacén, reduciendo significativamente los tiempos de búsqueda y recuperación de productos.
Una de las principales ventajas de estos sistemas es su capacidad para aprovechar eficientemente el espacio vertical. En almacenes con techos altos, los sistemas rotativos pueden extenderse hasta alturas considerables, multiplicando el espacio de almacenamiento disponible sin aumentar la huella del edificio. Esto resulta especialmente valioso en entornos urbanos donde el espacio es limitado y costoso.
Además, los sistemas de almacenamiento rotativo vertical ofrecen un control preciso del inventario. Cada bandeja o compartimento puede ser asignado a productos específicos, facilitando el seguimiento y la gestión del stock. Esta organización meticulosa no solo mejora la precisión del inventario, sino que también reduce el riesgo de pérdidas o daños a los productos almacenados.
Tipos de carruseles y estanterías rotativas: kardex, hänel, modula
En el mercado actual, existen diversos fabricantes y modelos de sistemas de almacenamiento rotativo, cada uno con sus características únicas. Tres de los nombres más reconocidos en la industria son Kardex, Hänel y Modula. Estos fabricantes ofrecen una amplia gama de soluciones adaptadas a diferentes necesidades y sectores industriales.
Carruseles horizontales: optimización del espacio en anchura
Los carruseles horizontales son sistemas de almacenamiento que rotan en un plano horizontal, similar a un carrusel de aeropuerto. Estos sistemas son ideales para productos de tamaño mediano y pequeño, y son especialmente eficientes en espacios con techos bajos pero con suficiente anchura disponible. Los carruseles horizontales permiten un acceso rápido a los productos y son excelentes para operaciones de picking de alto volumen.
Una de las ventajas clave de los carruseles horizontales es su capacidad para manejar múltiples pedidos simultáneamente. Los operarios pueden trabajar en varios pedidos a la vez, aumentando significativamente la productividad. Además, estos sistemas pueden integrarse fácilmente con software de gestión de almacenes para optimizar aún más los procesos de picking.
Carruseles verticales: aprovechamiento de la altura del almacén
Los carruseles verticales son la solución perfecta para almacenes con espacio limitado en planta pero con altura considerable. Estos sistemas consisten en una serie de bandejas que rotan verticalmente, llevando los productos al nivel del operario. Los carruseles verticales son extremadamente eficientes en términos de aprovechamiento del espacio, pudiendo almacenar una gran cantidad de productos en una huella relativamente pequeña.
Una característica destacada de los carruseles verticales es su velocidad de acceso. Gracias a motores potentes y sistemas de control avanzados, estos carruseles pueden entregar los productos al operario en cuestión de segundos. Esto resulta en una reducción significativa de los tiempos de picking y un aumento general de la productividad del almacén.
Estanterías rotativas paternoster: funcionamiento y aplicaciones
Las estanterías rotativas paternoster, también conocidas como sistemas paternoster, son una variación de los carruseles verticales. Su nombre proviene de su similitud con los rosarios utilizados en oraciones, ya que las bandejas circulan continuamente en un movimiento vertical. Estos sistemas son ideales para almacenar productos de diferentes tamaños y pesos en un espacio compacto.
El funcionamiento de un sistema paternoster es simple pero efectivo. Las bandejas están conectadas a una cadena que las mueve en un circuito cerrado. Cuando el operario solicita un producto, el sistema rota hasta que la bandeja correcta llega a la altura de trabajo. Esta rotación continua permite un acceso rápido a todos los productos almacenados.
Las aplicaciones de las estanterías rotativas paternoster son diversas. Son particularmente útiles en industrias como la farmacéutica, donde se requiere el almacenamiento de una gran variedad de productos pequeños, o en el sector automotriz para el almacenamiento de piezas y componentes.
Sistemas de almacenamiento rotativo de alta densidad
Los sistemas de almacenamiento rotativo de alta densidad representan la evolución más avanzada en este campo. Estos sistemas combinan las ventajas de los carruseles verticales y horizontales con tecnologías de automatización y control de última generación. El resultado es una solución de almacenamiento que maximiza tanto el espacio vertical como el horizontal, ofreciendo una densidad de almacenamiento sin precedentes.
Una característica distintiva de estos sistemas es su capacidad para adaptarse dinámicamente a las necesidades cambiantes del inventario. Utilizando algoritmos avanzados, pueden reorganizar automáticamente los productos para optimizar el espacio y los tiempos de acceso. Esto resulta especialmente valioso en entornos con fluctuaciones frecuentes en la demanda o con cambios estacionales en el inventario.
Los sistemas de almacenamiento rotativo de alta densidad pueden aumentar la capacidad de almacenamiento hasta en un 85% en comparación con los sistemas de estanterías tradicionales, al tiempo que reducen los tiempos de picking en más de un 65%.
Integración de software WMS con sistemas rotativos
La integración de sistemas de gestión de almacenes (WMS) con los sistemas de almacenamiento rotativo es fundamental para maximizar la eficiencia y el control del inventario. Esta sinergia entre hardware y software permite una gestión precisa y en tiempo real de todos los procesos logísticos, desde la recepción de mercancías hasta el despacho de pedidos.
Conexión con ERP y sistemas de gestión de inventario
La conexión entre los sistemas de almacenamiento rotativo y los sistemas ERP (Enterprise Resource Planning) de la empresa es crucial para mantener una visión integral de toda la cadena de suministro. Esta integración permite que la información fluya sin problemas entre los diferentes departamentos, desde compras hasta ventas, pasando por logística y finanzas.
Al integrar el WMS
con el ERP, se logra una sincronización automática de datos críticos como niveles de inventario, órdenes de compra y pedidos de clientes. Esto elimina la necesidad de entrada manual de datos, reduciendo errores y ahorrando tiempo valioso. Además, esta conexión facilita la toma de decisiones informadas en tiempo real, permitiendo ajustes rápidos en la estrategia de inventario y compras.
Picking guiado por luz y voz en almacenes rotativos
Los sistemas de picking guiado por luz (pick-to-light) y voz (pick-by-voice) son tecnologías complementarias que, cuando se integran con sistemas de almacenamiento rotativo, pueden aumentar significativamente la velocidad y precisión de las operaciones de picking. Estos sistemas utilizan indicadores luminosos o instrucciones de voz para guiar a los operarios hacia las ubicaciones exactas de los productos requeridos.
En un entorno de almacenamiento rotativo, el picking guiado por luz funciona iluminando los compartimentos específicos donde se encuentran los productos necesarios para un pedido. Esto reduce drásticamente el tiempo de búsqueda y minimiza los errores de selección. Por otro lado, el picking por voz permite a los operarios trabajar con las manos libres, recibiendo instrucciones audibles sobre qué productos recoger y en qué cantidades.
La combinación de estas tecnologías con los sistemas rotativos crea un entorno de trabajo altamente eficiente y ergonómico, donde los operarios pueden completar pedidos con una precisión cercana al 100% y una velocidad significativamente mayor que en los sistemas tradicionales.
Trazabilidad y control de stock en tiempo real
La trazabilidad y el control de stock en tiempo real son aspectos críticos en la gestión moderna de almacenes. Los sistemas de almacenamiento rotativo, cuando se integran con un WMS avanzado, ofrecen capacidades de seguimiento y control sin precedentes. Cada movimiento de producto, desde su recepción hasta su despacho, puede ser registrado y monitoreado con precisión milimétrica.
Esta visibilidad en tiempo real del inventario permite a las empresas:
- Reducir los niveles de inventario sin comprometer la disponibilidad de productos
- Identificar y resolver rápidamente discrepancias en el stock
- Implementar estrategias de rotación de inventario más eficientes, como FIFO (First In, First Out) o LIFO (Last In, First Out)
- Mejorar la precisión de las previsiones de demanda y las decisiones de reabastecimiento
Además, la trazabilidad avanzada es especialmente valiosa en industrias reguladas, como la farmacéutica o la alimentaria, donde el seguimiento detallado de lotes y fechas de caducidad es crucial para cumplir con normativas y garantizar la seguridad del consumidor.
Implementación de un sistema rotativo: pasos y consideraciones
La implementación de un sistema de almacenamiento rotativo es un proyecto significativo que requiere una planificación cuidadosa y una ejecución metódica. A continuación, se detallan los pasos clave y las consideraciones importantes para asegurar una implementación exitosa.
Análisis de flujos y productos para seleccionar el sistema adecuado
El primer paso crucial en la implementación de un sistema rotativo es realizar un análisis exhaustivo de los flujos de trabajo actuales y las características de los productos que se almacenarán. Este análisis debe considerar factores como:
- Volumen y frecuencia de movimientos de productos
- Tamaño, peso y forma de los artículos a almacenar
- Patrones de demanda y estacionalidad
- Requisitos especiales de almacenamiento (temperatura, humedad, etc.)
- Proyecciones de crecimiento futuro
Con esta información, se puede seleccionar el tipo de sistema rotativo más adecuado, ya sea un carrusel horizontal, vertical o un sistema paternoster. La elección correcta del sistema es fundamental para maximizar la eficiencia y el retorno de la inversión.
Diseño y configuración de bandejas y compartimentos
Una vez seleccionado el tipo de sistema, el siguiente paso es diseñar la configuración interna de bandejas y compartimentos. Esta fase es crítica para optimizar el uso del espacio y facilitar el acceso a los productos. Se deben considerar aspectos como:
La altura y profundidad de las bandejas deben adaptarse a los productos específicos que se almacenarán. Es importante considerar no solo las dimensiones actuales de los productos, sino también posibles cambios futuros en el inventario. La configuración de compartimentos dentro de las bandejas debe ser flexible para acomodar diferentes tamaños de productos y permitir ajustes según las necesidades cambiantes.
Además, se debe prestar atención a la ergonomía y la seguridad. Las bandejas deben diseñarse de manera que los productos sean fácilmente accesibles para los operarios, minimizando el riesgo de lesiones por esfuerzos repetitivos o manipulación inadecuada de cargas.
Instalación y puesta en marcha: protocolos y tiempos
La fase de instalación y puesta en marcha es un momento crítico en la implementación de un sistema de almacenamiento rotativo. Es esencial establecer protocolos claros y calendarios realistas para minimizar las interrupciones en las operaciones del almacén. Los pasos típicos en esta fase incluyen:
- Preparación del espacio físico, incluyendo cualquier modificación necesaria en la infraestructura existente
- Instalación del hardware del sistema rotativo
- Configuración y prueba del software de control
- Integración con sistemas WMS y ERP existentes
- Carga inicial de productos en el sistema
- Pruebas exhaustivas de funcionamiento y rendimiento
El tiempo necesario para la instalación y puesta en marcha puede variar significativamente dependiendo de la complejidad del sistema y el tamaño del almacén. Es común que este proceso tome entre 2 y 8 semanas para sistemas de tamaño medio, aunque proyectos más grandes pueden requerir varios meses.
Formación del personal en el uso de sistemas rotativos
La formación adecuada del personal es crucial para el éxito a largo plazo de un sistema de almacenamiento rotativo. Los operarios deben estar completamente familiarizados con el funcionamiento del sistema, los procedimientos de seguridad y las mejores prácticas para maximizar la eficiencia. Un programa de formación integral debe incluir:
Sesiones teóricas sobre los principios de funcionamiento del sistema rotativo y su integración con el WMS. Entrenamiento práctico en la operación del sistema, incluyendo procedimientos de carga y descarga, navegación del software y resolución de problemas básicos. Formación en seguridad, incluyendo protocolos de emergencia y mantenimiento preventivo básico.
Es recomendable implementar un enfoque de “formación de formadores”, donde se capacita a un grupo core de empleados que luego pueden transmitir sus conocimientos a otros miembros del equipo. Esto ayuda a crear una cultura de mejora continua y facilita la adaptación a futuras actualizaciones o cambios en el sistema.
Una formación efectiva puede reducir los errores operativos en hasta un 70% y aumentar la productividad del personal en más de un 30% durante los primeros meses de uso del nuevo sistema.
Optimización de procesos logísticos con almacenamiento rotativo
Reducción de tiempos de picking y preparación de pedidos
Los sistemas de almacenamiento rotativo ofrecen una reducción significativa en los tiempos de picking y preparación de pedidos. Al traer los productos directamente al operario, se eliminan los desplazamientos innecesarios por el almacén. Un carrusel vertical puede reducir el tiempo de picking hasta en un 65% en comparación con los métodos tradicionales. ¿Cómo se logra esta mejora tan drástica?
La clave está en la combinación de movimiento automatizado y software inteligente. El sistema identifica la ubicación exacta del producto requerido y lo entrega en segundos al punto de acceso del operario. Esto no solo acelera el proceso, sino que también reduce la fatiga del trabajador, permitiendo mantener altos niveles de productividad durante períodos más largos.
Maximización del espacio de almacenamiento disponible
Una de las ventajas más notables de los sistemas rotativos es su capacidad para maximizar el espacio de almacenamiento disponible. Estos sistemas pueden aprovechar la altura total del almacén, utilizando espacios que tradicionalmente quedarían desaprovechados. Un carrusel vertical típico puede almacenar el equivalente a 100 metros lineales de estanterías convencionales en tan solo 10 metros cuadrados de espacio en planta.
Esta optimización del espacio no solo permite almacenar más productos en la misma área, sino que también libera espacio valioso para otras actividades operativas. Imagine poder duplicar su capacidad de almacenamiento sin necesidad de expandir físicamente su almacén. ¿Cómo impactaría esto en la eficiencia y rentabilidad de su negocio?
Mejora de la ergonomía y seguridad laboral
Los sistemas de almacenamiento rotativo no solo optimizan el espacio y el tiempo, sino que también contribuyen significativamente a la mejora de la ergonomía y la seguridad laboral. Al traer los productos al operario a una altura de trabajo óptima, se reducen los movimientos repetitivos y las posturas incómodas que pueden causar lesiones a largo plazo.
Esta mejora en la ergonomía se traduce en beneficios tangibles para la empresa:
- Reducción de lesiones y bajas laborales
- Aumento de la satisfacción y retención del personal
- Mejora de la productividad a largo plazo
- Cumplimiento de normativas de seguridad laboral
Además, al eliminar la necesidad de que los operarios suban escaleras o utilicen equipos de elevación para acceder a productos en alturas, se reduce significativamente el riesgo de accidentes en el almacén.
Disminución de errores en la gestión de inventario
La implementación de sistemas de almacenamiento rotativo, en conjunto con software WMS avanzado, permite una disminución drástica de los errores en la gestión de inventario. Estos sistemas ofrecen un control preciso sobre la ubicación y cantidad de cada producto, eliminando prácticamente las discrepancias de inventario.
La precisión mejorada se logra a través de:
- Asignación automática de ubicaciones para cada producto
- Seguimiento en tiempo real de movimientos de inventario
- Verificación automática durante los procesos de picking y reposición
- Alertas de stock bajo o discrepancias de inventario
Esta reducción de errores no solo mejora la eficiencia operativa, sino que también aumenta la satisfacción del cliente al garantizar la disponibilidad y entrega precisa de los productos solicitados.
Mantenimiento y actualización de sistemas de almacenamiento rotativo
Programas de mantenimiento preventivo para carruseles
El mantenimiento preventivo es crucial para garantizar el funcionamiento óptimo y la longevidad de los sistemas de almacenamiento rotativo. Un programa de mantenimiento bien estructurado puede prevenir averías costosas y minimizar los tiempos de inactividad. ¿Qué elementos clave debe incluir un programa de mantenimiento efectivo?
Los componentes esenciales de un programa de mantenimiento preventivo incluyen:
- Inspecciones regulares de componentes mecánicos y eléctricos
- Lubricación de partes móviles según las especificaciones del fabricante
- Verificación y ajuste de tensiones en cadenas y correas
- Limpieza de sensores y sistemas de control
- Actualización de firmware y software de control
Es recomendable establecer un calendario de mantenimiento basado en las horas de operación o ciclos de uso, en lugar de fechas fijas. Esto asegura que el mantenimiento se realice cuando realmente es necesario, optimizando costos y tiempos de inactividad.
Actualizaciones de software y hardware para mejorar rendimiento
La tecnología en el campo de la logística y el almacenamiento evoluciona rápidamente. Para mantener la competitividad y eficiencia de su sistema de almacenamiento rotativo, es esencial considerar actualizaciones periódicas tanto de software como de hardware.
Las actualizaciones de software pueden incluir nuevas funcionalidades en el sistema de control, mejoras en la interfaz de usuario o integraciones más avanzadas con sistemas WMS y ERP. Por otro lado, las actualizaciones de hardware pueden implicar la sustitución de componentes por versiones más eficientes o la adición de nuevos módulos para expandir la capacidad o funcionalidad del sistema.
Al evaluar las opciones de actualización, considere:
- El impacto potencial en la productividad y eficiencia
- La compatibilidad con sus sistemas existentes
- El retorno de inversión esperado
- Los requisitos de formación para el personal
Recuerde que una actualización bien planificada puede extender significativamente la vida útil de su sistema y mejorar su rendimiento global.
Diagnóstico y resolución de problemas comunes
A pesar del mantenimiento preventivo, ocasionalmente pueden surgir problemas en los sistemas de almacenamiento rotativo. Contar con un protocolo claro para el diagnóstico y resolución de problemas es esencial para minimizar los tiempos de inactividad y mantener la eficiencia operativa.
Algunos problemas comunes y sus posibles soluciones incluyen:
Problema | Posible causa | Solución |
---|---|---|
El carrusel no rota | Fallo en el motor o sensor de posición | Verificar conexiones eléctricas y reemplazar componentes si es necesario |
Errores de posicionamiento | Desajuste en el sistema de control | Recalibrar sensores y actualizar software de control |
Ruido excesivo durante la operación | Falta de lubricación o desgaste de componentes | Realizar mantenimiento y reemplazar piezas desgastadas |
Es fundamental capacitar al personal de mantenimiento en la identificación y resolución de estos problemas comunes. Además, contar con un stock de repuestos críticos y un contrato de servicio con el proveedor del sistema puede ayudar a reducir significativamente los tiempos de inactividad en caso de averías más complejas.
Un sistema de almacenamiento rotativo bien mantenido y actualizado puede operar eficientemente durante más de 20 años, proporcionando un excelente retorno de inversión a largo plazo.
Al implementar estas estrategias de mantenimiento y actualización, su sistema de almacenamiento rotativo no solo mantendrá su rendimiento óptimo, sino que también se adaptará a las cambiantes necesidades de su negocio, asegurando que su inversión continúe ofreciendo beneficios a largo plazo.